Au Québec, l’ossature légère en bois est le principal système structural utilisé dans la construction de petits bâtiments.
Au cours des dernières années, la réglementation a évolué pour permettre son usage dans les bâtiments multi résidentiels de cinq et six étages. Mais est-ce que ce système pourrait être adapté pour étendre son utilisation à des bâtiments de grande hauteur? C’est avec l’objectif de répondre à cette question que Nicolas Labrecque a réalisé un projet de maîtrise à l’Université Laval.
Ce projet s’inscrit dans le cadre de l’Initiative sur la construction industrialisée (ICI), qui découle de la Chaire industrielle de recherche sur la construction écoresponsable en bois (CIRCERB). Il a été réalisé sous la direction de M. Pierre Blanchet, professeur au Département des sciences du bois et de la forêt de l’Université Laval, et sous la codirection de M. Sylvain Ménard, professeur au Département des sciences appliquées de l’Université du Québec à Chicoutimi et de M. Marc Oudjene, professeur au Département de génie civil et de génie des eaux de l’Université Laval.
L’objectif principal de la recherche était donc de concevoir un système structural permettant d’atteindre les performances structurelles requises pour l’utilisation de l’ossature légère dans les bâtiments de grande hauteur entre 10 et 20 étages. Le projet cherchait également à tirer profit des avantages de la construction préfabriquée modulaire à ossature légère qui permet un niveau élevé de préfabrication. L’isolation, les éléments mécaniques et électriques, les revêtements, les portes, les fenêtres, les finitions des murs et des planchers et même les meubles et les appareils électroménagers peuvent être installés en usine, ce qui diminue le travail à accomplir sur place.
Le concept proposé
Le système proposé par l’étudiant est composé d’une hyperstructure supportant les charges de sous-structures superposées de quatre étages en ossature légère. Plus spécifiquement, deux types d’hyperstructures de 20 étages, dont une en lamellé-collé et une en béton, ont été conçues selon le Code national du bâtiment du Canada 2015. Leur comportement structural a été comparé. Pour y arriver, une méthode numérique pour la modélisation par éléments finis d’ossature légère modulaire a été développée. Il a été ainsi possible d’étudier l’interaction entre l’hyperstructure et les sous-structures modulaires ainsi que leur impact mutuel.
FIGURE 1
Treillis verticaux en lamelé-collé Noyau central et dalles en béton
Figure 1 – Les deux types d’hyperstructures testées
FIGURE 2
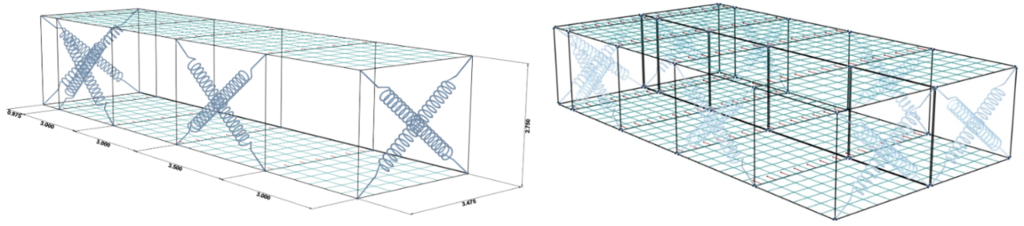
Figure 2 – Modélisation 3D des modules en ossature légère
FIGURE 3
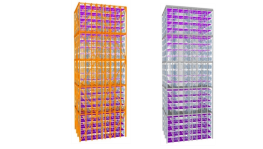
Figure 3 – Les hyperstructures, en lamellé-collé (à gauche) et en béton (à droite), dans lesquelles ont été insérées les sous-structures modulaires en ossature légère en bois
La mise à l’épreuve
L’interaction entre les deux systèmes et l’impact sur les sous-structures ont été analysés. Les résultats démontrent que le système en béton peut permettre d’atteindre les performances requises si les sous-structures modulaires sont connectées à tous les étages à l’hyperstructure. Pour le concept en lamellé-collé, les performances requises peuvent être atteintes en connectant les sous-structures à chaque étage, mais aussi en ne les connectant que par la base aux planchers de l’hyperstructure. Les résultats démontrent également que les efforts transmis aux murs de refend en ossature légère sont dans tous les cas réalistes. Ces efforts peuvent être repris par des compositions de murs de refend communes. Les configurations conventionnelles des murs de cisaillement sont suffisantes pour résister au cisaillement des charges gravitationnelles, de vent et sismiques.
On doit noter que ces résultats ont été calculés pour une seule région géographique, ils ne peuvent pas être exportés partout sans que cette particularité soit prise en considération. Cependant, les charges sismiques, de vent et de neige de la ville de Québec étant assez élevées, les résultats devraient être conservateurs pour plusieurs régions canadiennes. De plus, les connexions des hyperstructures n’ont pas été considérées dans cette étude, mais leur conception pourrait être critique dans un tel système. Dans les modèles, la plupart des connexions ont été considérées comme entièrement rotulées ou rigides et une étude sur l’impact du degré de rigidité pourrait être pertinente. Pour mieux comprendre les propriétés dynamiques de ces systèmes structuraux, l’implémentation d’un modèle de murs de refend hystérétique serait de plus nécessaire. Finalement, un aspect critique dans la conception de bâtiments de grande hauteur, la résistance au feu, n’a pas été étudié, mais devrait l’être pour une preuve de concept adéquate.
Installation au chantier
Les sous-structures modulaires en ossature légère étant hautement préfabriquées, la facilité de préfabrication de l’hyperstructure et la rapidité d’érection du bâtiment seraient des avantages importants pour un tel système. La Figure 4 montre les étapes de l’érection du système structural.
Les étapes 2 à 6 sont similaires pour tous les concepts d’hyperstructures. Elles peuvent différer selon le type de connexion entre les éléments préfabriqués, mais ce sujet n’a pas été étudié dans le cadre de ce projet. L’étape 1, le coulage sur place des noyaux de béton, est un inconvénient majeur pour la vitesse d’érection du bâtiment pour le système en béton. Un temps de construction plus long implique une perte de revenus pour le propriétaire du bâtiment, des frais d’intérêt plus élevés et plus de perturbations pour la localité et les entreprises voisines. (R. Mark Lawson et al., 2012).
FIGURE 4
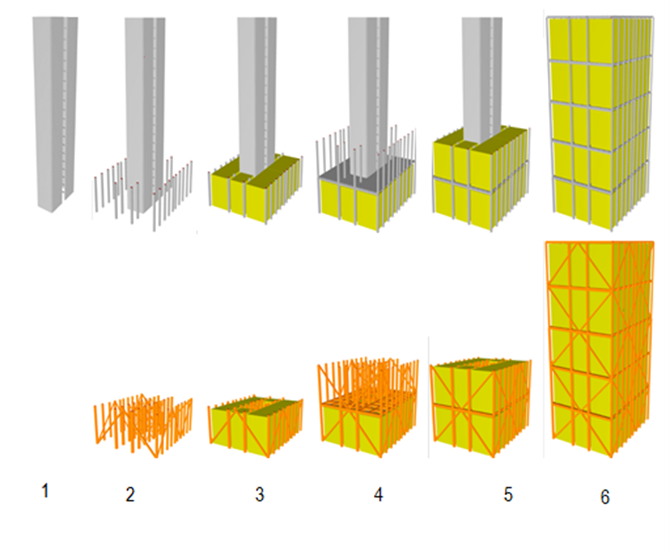
Figure 4 – Les étapes de montage avec noyaux en béton (en haut) et pour le concept en lamellé-collé (en bas). L’étape 1 est le moulage des noyaux de béton. L’étape 2 est l’assemblage des colonnes et diagonales des quatre premiers étages. L’étape 3 est le levage en place et la connexion des sous-structures modulaires (en jaune). L’étape 4 est la mise en place des cassettes du premier hyperplancher et des colonnes et diagonales des étages 4 à 8. L’étape 5 est le levage en place et la connexion des sous-structures modulaires. L’étape 6 est la répétition des étapes 4 à 5 jusqu’à l’achèvement.
Conclusion
Enfin, pour répondre à la fois à la croissance de la population urbaine mondiale et aux changements climatiques, de nouveaux systèmes structuraux à haut niveau de préfabrication et utilisant des matériaux renouvelables doivent être développés. L’idée proposée par Nicolas Labrecque, soit un système d’unités primaires qui peuvent s’empiler les unes sur les autres pour former une tour multiétagée, a été pensée en ce sens.
Les modèles et analyses développés dans ce projet participent à l’ajout de méthodes possibles pour construire des bâtiments en bois en utilisant la préfabrication au maximum. Le fait de développer des solutions permettant l’utilisation de l’ossature légère dans des bâtiments de grande hauteur pourrait potentiellement participer à l’augmentation de la hauteur limite actuelle et permettre au secteur de la construction en bois de s’industrialiser davantage dans des marchés qui appartiennent traditionnellement plus au béton et à l’acier. Ces nouveaux concepts structuraux pourraient permettre éventuellement d’augmenter la rapidité d’érection, de favoriser la qualité des composantes et des travaux, de diminuer les coûts de construction et d’augmenter l’utilisation de produits structuraux renouvelables dans les centres urbains.
Références
Lawson, R. Mark, Ogden, R. G., & Bergin, R. (2012). Application of Modular Construction in High-Rise Buildings. Journal of Architectural Engineering, 18(2), 148–154.
http://doi.org/10.1061/(ASCE)AE.1943-5568.0000057
Collaboration spéciale de la Chaire industrielle de recherche sur la construction écoresponsable en bois (CIRCERB) de l’Université Laval.